5月9日,由中核華興承建的國內首個采用無粘結預應力體系的核島安全殼——田灣核電項目7號機組核島安全殼預應力工程圓滿完工,為后續殼間安裝工作創造了有利條件,標志著中核華興核電預應力施工技術水平再次躍上新臺階。中核華興牢記習近平總書記關于“樹立全球核能合作典范”“打造核安全領域全球標桿”的殷切囑托,響應中核集團號召,積極培育新質生產力,不斷塑造發展新動能、新優勢,為我國核工業高質量發展貢獻華興力量。
新工藝,開創預應力施工工藝先河
預應力與外殼穹頂同步施工的方法首次應用于田灣核電項目7號機組核島,即先吊裝外殼鋼底模,再進行內殼預應力施工的新工藝步驟。田灣項目部積極發揮“大項目部”管理優勢,針對VVER-1200堆型在國內首次應用無粘結預應力體系成立聯合科研小組,組織專業技術人員開展技術攻關和無粘結預應力系統施工工藝研究,研究制定了詳細的專項進度計劃和施工方案,通過預應力張拉平臺分階段提前安裝,達到水平張拉設備提前預引入、水平鋼束灌漿及張拉作業后施工的目的,同時采用單根千斤頂技術進行穹頂段水平鋼束的精密張拉作業,為在殼間開展內殼張拉作業創造有利條件,做到預應力施工與外穹頂施工同步施工,實現外殼穹頂與預應力施工解耦,開辟出4個月的寶貴窗口期,為穹頂上部非能動水箱按期完工奠定了基礎,有力助推核電建造“工期更短、成本更低、質量更優”的目標實現。
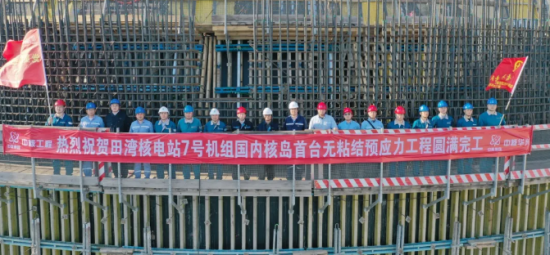
新技術,
為中俄核能合作典范項目保駕護航
國內首個無粘結預應力工程一級里程碑如期實現。中核華興以創新思維和務實舉措推動“整體·協同”年專項行動走深走實,田灣項目部組織召開預應力系統交流會,以目標導向、問題導向、結果導向,用協同的方法解決施工過程中重點難點問題,預應力團隊以廖春生創新工作室為依托,對施工過程中“難點”“堵點”問題進行專項技術攻關突破,形成并掌握了大直徑預應力管道制作及安裝、無粘結預應力鋼絞線單根穿束及整體穿束、成品灌漿料研發與應用、預應力先灌漿后張拉等一系列無粘結預應力施工新技術,為田灣核電項目7號機組核島提供強有力的技術保障。
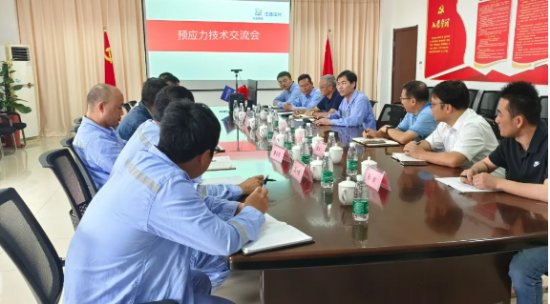
新設備,促進工效大幅提升
新設備的首次應用為預應力施工效率提升發揮巨大效能。田灣核電項目7號機組核島無粘結預應力工程采用了多項自主研發的國產化裝備,包括無粘結預應力穿束設備、1500T千斤頂、小型化張拉千斤頂及油泵等,已達到進口同類設備的性能要求。這些設備為預應力施工效率提升、工期大幅縮短發揮了極為關鍵的作用,充分驗證了公司預應力設備性能穩定性以及適應新堆型的可靠性,為公司設備國產化奠定堅實基礎。
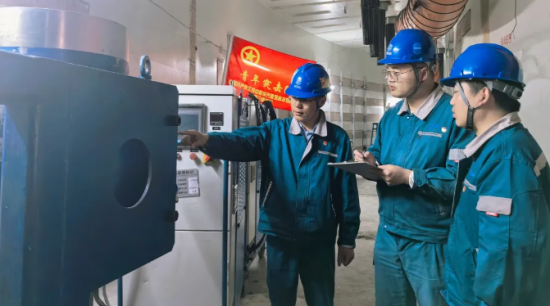
新材料,助力項目質量提質增效
成品灌漿料用于孔道灌漿為國內首次應用,為公司在核電預應力工程施工質量上提質增效。田灣核電項目7號機組核島在施工過程中進行灌漿實驗時發現,水泥和外加劑性能不匹配導致漿體參數波動、水泥漿體運輸距離遠、制漿工藝效率低的問題,無粘結預應力鋼束孔道直徑為220mm,為目前核電預應力孔道直徑之最,漿體灌注需量大大增加。為解決灌漿問題,田灣項目部與預應力項目團隊聯合開展成品灌漿料應用技術攻關,通過了漿體上機接收試驗及灌漿試驗驗證,各項技術指標滿足設計要求。憑借其簡便的漿體配制流程、良好的流動性和卓越的早期強度,將預應力灌漿的施工效率顯著提升30%以上,同時確保了灌漿質量的穩定可靠。
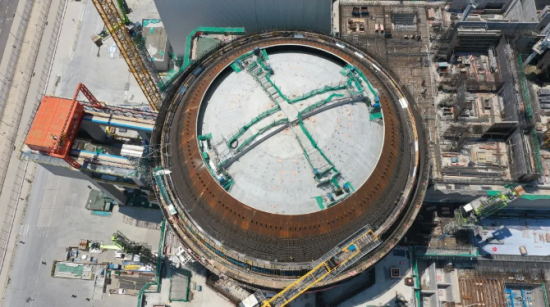
下一步,中核華興將繼續在核電建造領域緊抓“效能提升”與“創新激發”,進一步推動核電建造技術水平提升,為“打造核安全領域全球標桿”貢獻華興力量,以優異的成績迎接我國第一顆原子彈爆炸60周年、核工業創建70周年。