5月12日,由我國自主設計建造的亞洲首艘圓筒型“海上油氣加工廠”——“海葵一號”在山東青島離港啟運,將通過“大船背小船”的方式運往珠江口盆地的流花油田,為我國首個深水油田二次開發項目年內投產奠定基礎。
總臺央視記者 張叢婧:這里是青島膠州灣,我現在就在“海葵一號”裝船作業的現場。從今天早上五點開始出港,現在“海葵一號”已經成功搭乘上了 “新光華號”半潛船。光是裝船,就持續了三個多小時,我們也記錄下了全過程。現在大家看到的畫面,就是最精彩的進船過程,四條拖輪和半潛船的四條交叉纜繩,正從不同方向精確控制著“海葵一號”的龐大身軀,緩緩抵達預定位置,這個過程就像是“穿針引線”一樣。而且進船的兩側間隙誤差和就位精度,都要求控制在50毫米以內,在波濤洶涌的大海上,要完成這樣的高精度操作,是非常難的。可以看到,目前半潛船正在緩緩上浮,等甲板全部浮出水面后,還將進行裝船固定等后續作業,從而保證它在海上運輸過程中即使遇到大的風浪也能夠安全穩定。
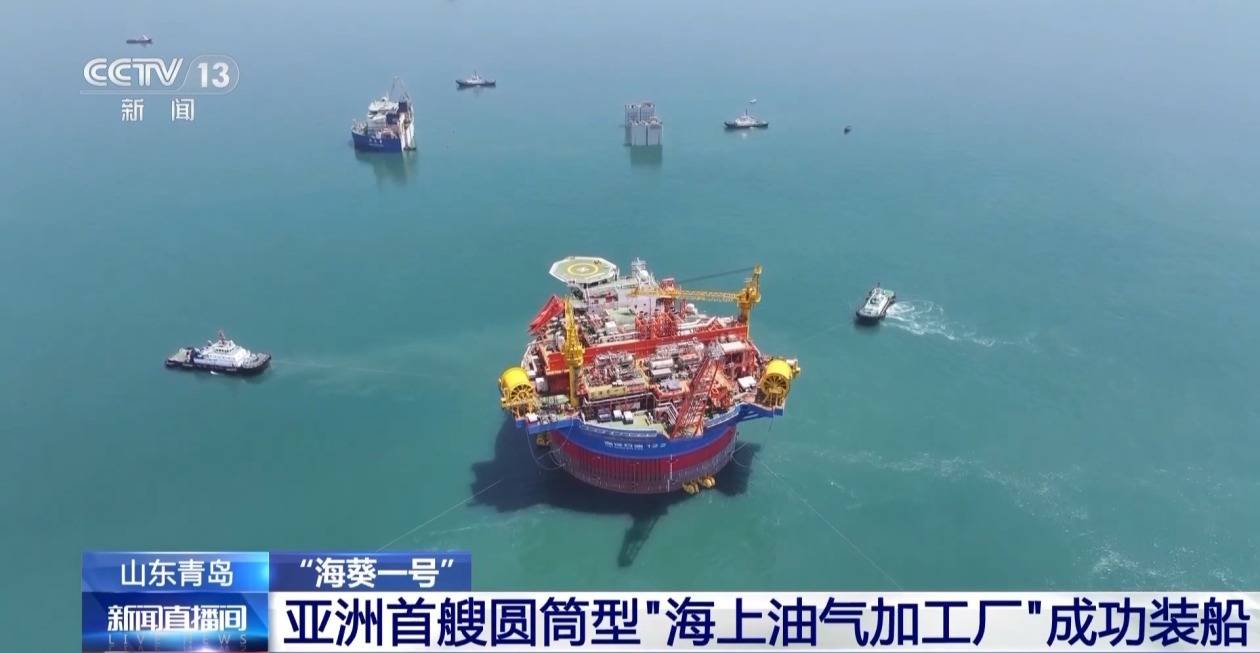
“海葵一號”裝船完成后,將于近日運往珠江口盆地流花油田進行安裝,航行距離超過1200海里,安裝完成后漂浮在水深324米的大海上工作,每天能處理約5600噸原油。
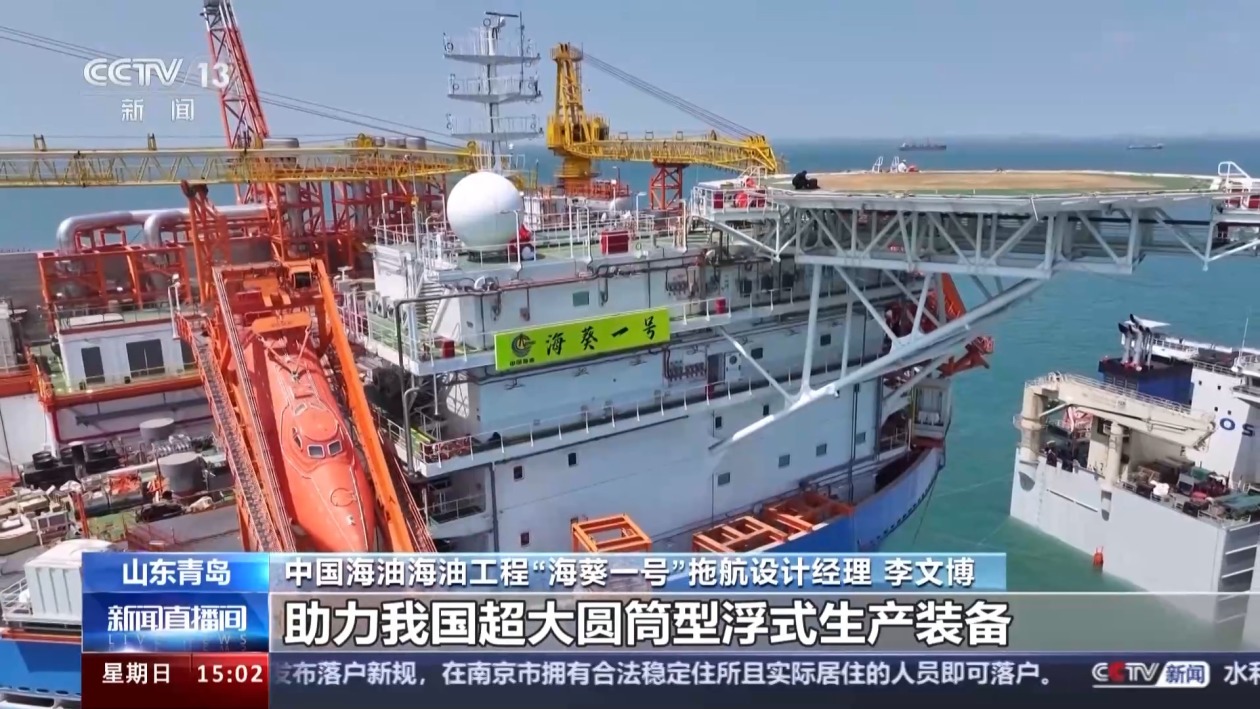
中國海油海油工程“海葵一號”拖航設計經理 李文博:我們首次在國內海洋裝備裝船中自主應用水下定位技術,確保“海葵一號”精準裝船就位,獨立完成技術方案編制、復雜計算分析、施工指揮管理等系列工作,助力我國超大圓筒型浮式生產裝備裝船拖航技術實現全流程自主化。
裝船難在哪兒?
由于超大、超重,且圓筒型結構受風面大,極易發生旋轉,裝船是“海葵一號”運輸中技術難度最大、作業風險最高的關鍵環節。
“海葵一號”主甲板面積相當于13個標準籃球場,高度接近30層樓,總重相當于3萬輛小汽車,把這樣一艘海上巨無霸裝載到船上,對方案設計、計算分析、現場指揮等均提出異常苛刻的要求。

中國海油海油工程“海葵一號”安裝項目經理 王繼強:“海葵一號”重量大,吃水深度接近航道極限,每月滿足作業條件的海況窗口僅有3天,不允許出任何差錯。裝船過程需要6艘港作拖輪密切配合,在流速湍急的海面上“穿針引線”,就位精度要求達到毫米級,且過程中不允許發生任何碰撞,技術難度創行業同類裝船作業之最。
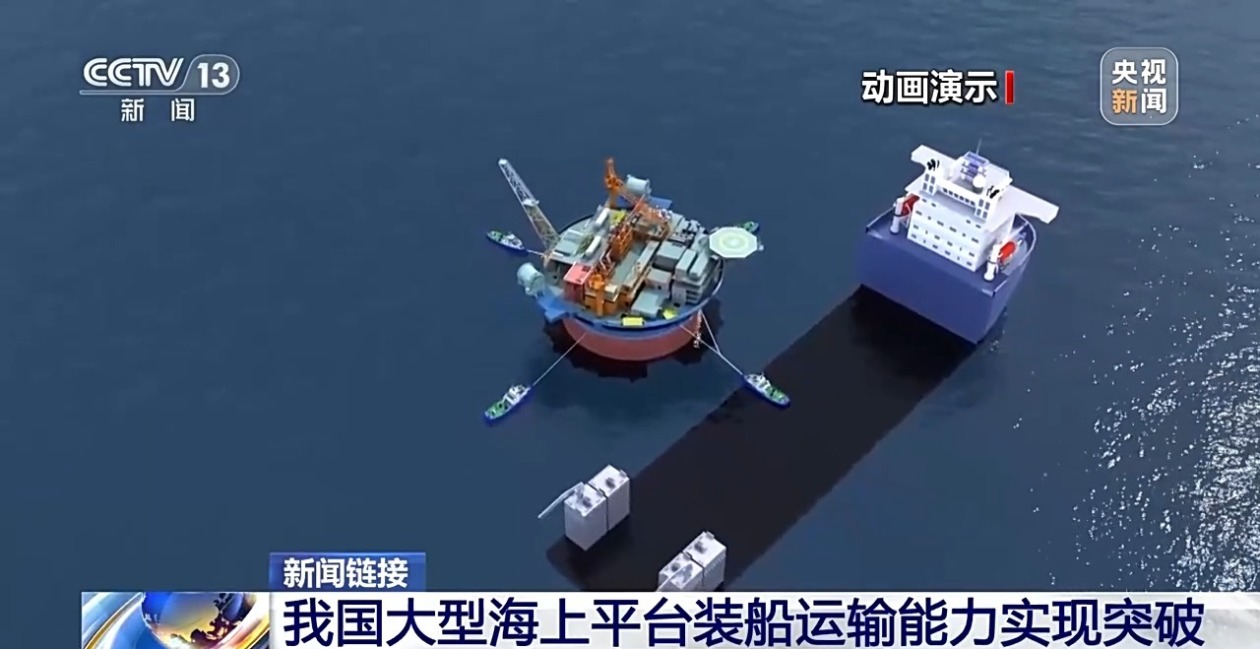
裝船作業過程中,半潛船甲板面將下潛到水下25米,完成就位后半潛船甲板再慢慢排載浮出水面托起“海葵一號”。裝船作業完成后,“海葵一號”將在半潛船甲板上進行連接固定,然后運送到我國珠江口海域的流花油田群。
我國大型海上平臺裝船運輸能力實現突破
裝船運輸是海上油氣田建設中必不可少的關鍵環節,隨著海洋平臺不斷向深水化、大型化發展,對裝船運輸裝備技術能力提出了更高要求。經過近些年的高速發展,我國大型海上平臺裝船運輸能力實現重要突破。
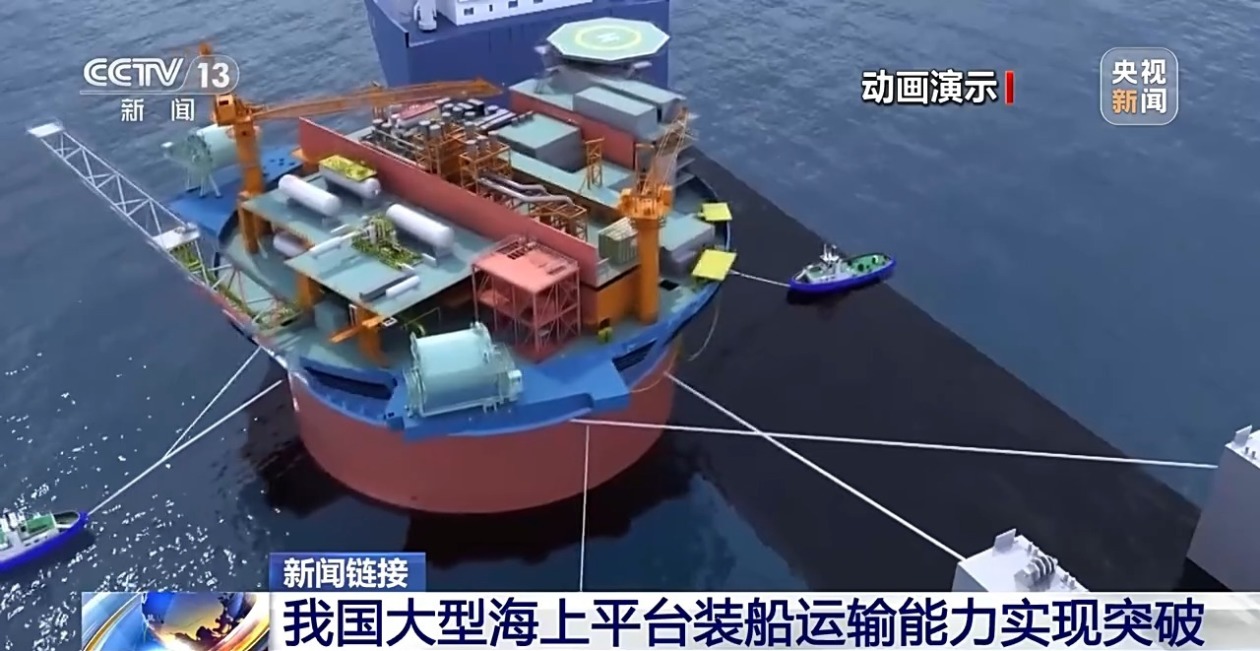
“海葵一號”裝船在國內海洋平臺裝船中首次成功應用水下精確定位技術,就位精度達到世界先進水平,本次裝船涉及的技術方案、計算分析、操作控制等全部由我國獨立完成,開創了我國全流程自主實施超大圓筒型浮式生產裝備裝船作業的先河。
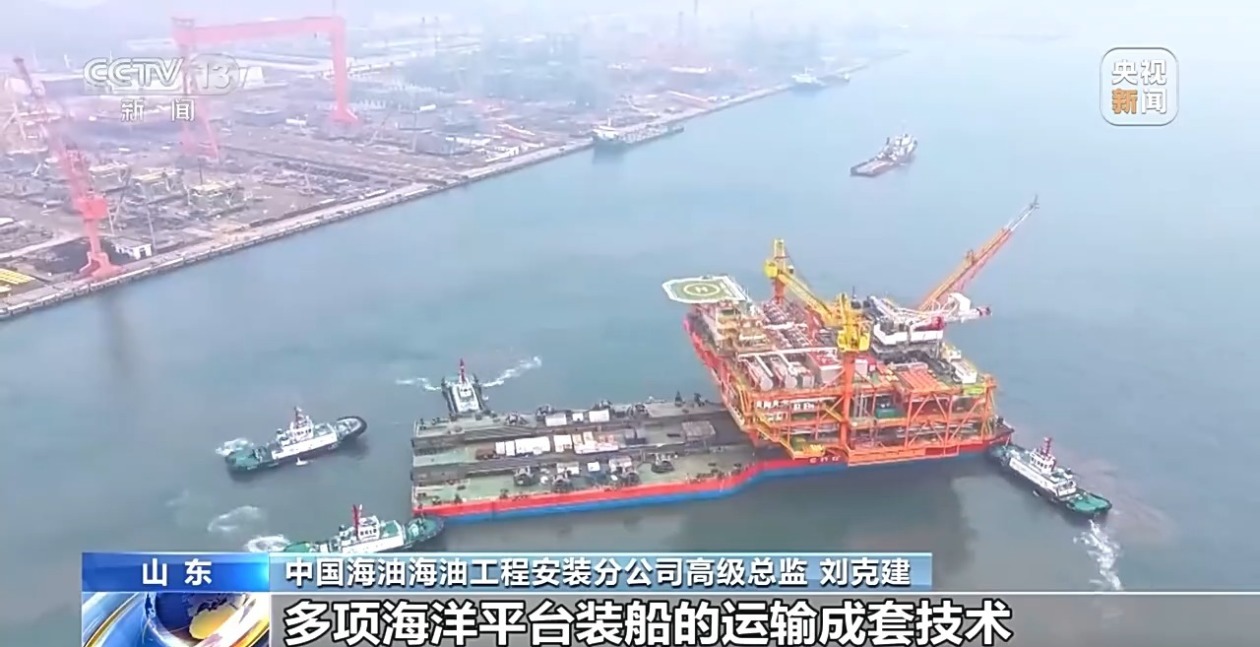
中國海油海油工程安裝分公司高級總監 劉克建:完成了近700次的大中型海洋平臺裝船作業,總重超過300萬噸,具備了35萬噸級浮式生產裝備浮裝、12000海里遠洋運輸等關鍵能力,系統掌握了牽引裝船、模塊化運輸車裝船、浮托裝船等多類型海洋平臺裝船運輸成套技術。
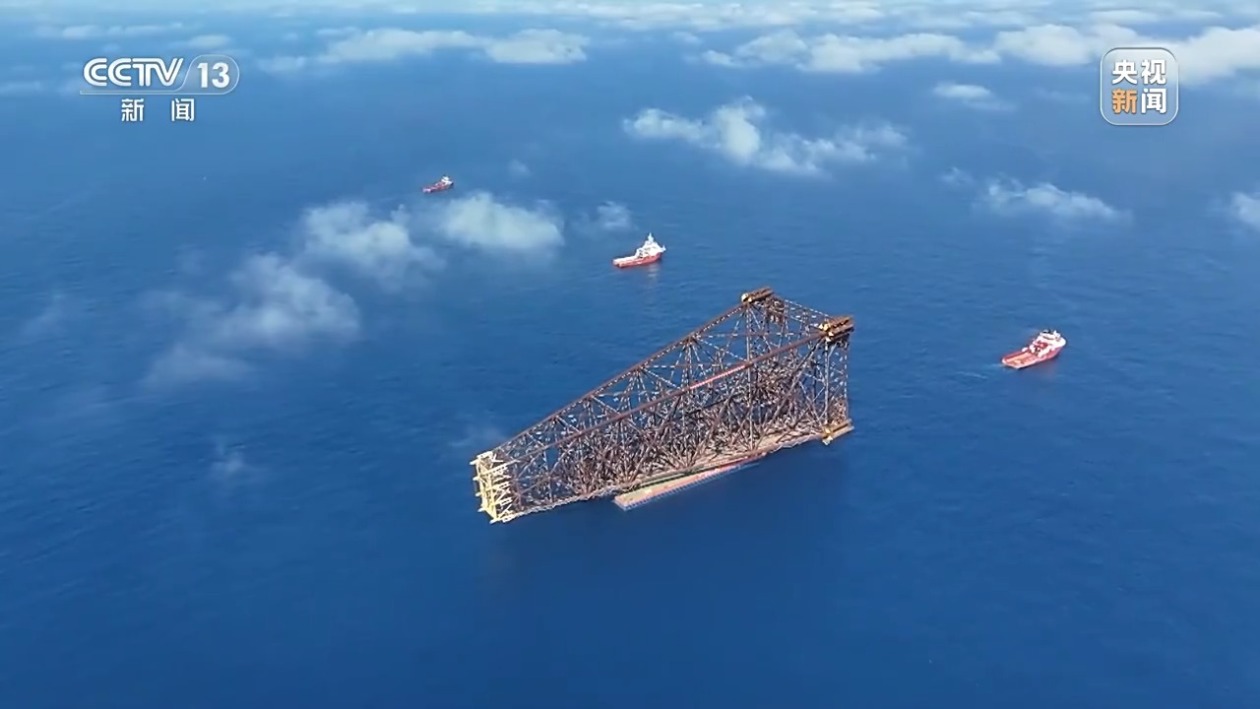
近年來,我國建成了亞洲最大海洋平臺運輸下水駁船“海洋石油229”、世界第二大半潛船“新光華號”等一批大型運輸船舶裝備。隨著“海基一號”“海基二號”“深海一號”等超大型海洋工程成功實施,我國裝船運輸技術已躍居世界先進水平。